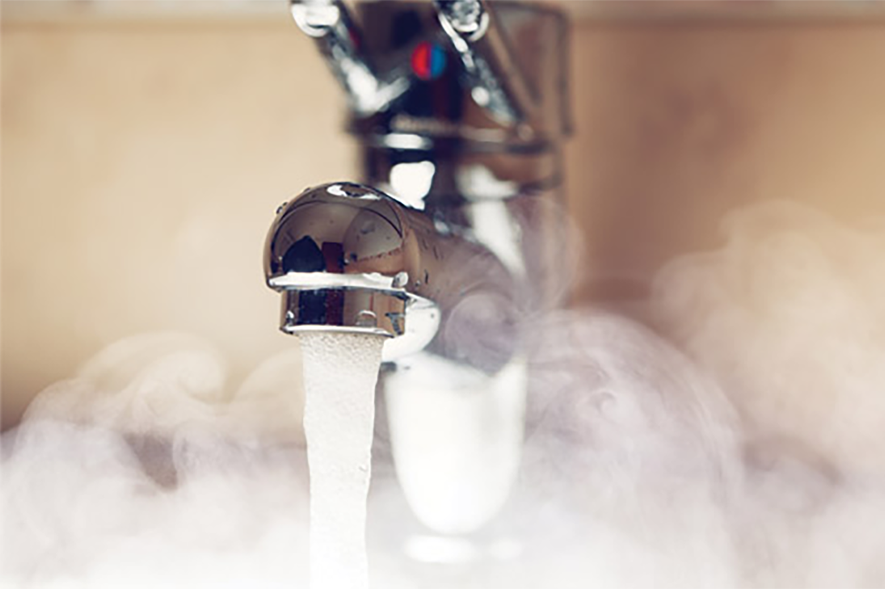
Heat and Cooling Systems
Boilers:
Industrial boilers are large, powerful, and
specialized vessels used to generate steam or hot water for various industrial
processes. They are commonly found in industries such as manufacturing, power
generation, chemical processing, refineries, and food processing. Industrial boilers
play a vital role in providing heat, powering machinery, and facilitating
various industrial operations. Industrial boilers come in different types, each
designed for specific applications and operating conditions.
Here are some key aspects of industrial
boilers:
·
Fire-Tube Boilers:
These boilers have a large cylindrical shell with fire tubes running through
it. Hot gases produced by the combustion process pass through the tubes,
heating the surrounding water.
·
Water-Tube Boilers:
In water-tube boilers, water flows through tubes while combustion gases
surround them. These boilers are known for their higher pressure and capacity,
making them suitable for high-demand applications.
·
Package Boilers:
Package boilers are pre-engineered and factory-assembled units, designed for
quick installation and compact footprint. They are often used in smaller
industrial applications.
·
Electric Boilers:
Electric boilers use electricity as the heating source to generate steam or hot
water. They are commonly used in areas where fossil fuel combustion is
undesirable or unavailable.
Fuel Sources: Industrial boilers can be fueled
by various energy sources, including:
·
Natural Gas: Natural
gas is a common fuel choice due to its availability, cost-effectiveness, and
relatively low emissions.
·
Oil: Heavy fuel oil
(HFO), light fuel oil (LFO), or diesel oil can be used as an alternative to
natural gas.
·
Coal: Coal-fired
boilers are still used in some industries, although their usage has decreased
due to environmental concerns.
·
Biomass: Biomass
boilers utilize organic materials such as wood pellets, agricultural residues,
or dedicated energy crops as fuel.
·
Renewable Energy
Sources: Some industrial boilers are designed to use renewable energy sources
such as solar thermal energy or geothermal energy.
Boiler Components: Industrial boilers consist
of several key components, including:
·
Combustion Chamber:
It is where the fuel is burned, releasing heat energy.
·
Heat Exchanger: The
heat exchanger transfers the heat from the combustion gases to the water,
generating steam or hot water.
·
Burners: Burners are
responsible for the controlled combustion of fuel, providing the necessary heat
for the boiler.
·
Control Systems:
Boilers are equipped with sophisticated control systems to regulate fuel and
air supply, maintain desired operating conditions, and ensure safety.
·
Safety Devices:
Industrial boilers are equipped with safety devices such as pressure relief
valves, water level indicators, and flame safeguards to prevent accidents and
ensure safe operation.
Efficiency and Emissions: Industrial
boilers strive for high efficiency to optimize energy consumption and reduce
operating costs. Efforts are made to minimize emissions of pollutants such as
nitrogen oxides (NOx), sulfur oxides (SOx), and particulate matter to comply
with environmental regulations.
Industrial boilers require proper
installation, regular maintenance, and adherence to safety protocols to ensure
safe and efficient operation. They are subject to local regulations and codes
that govern their design, installation, operation, and maintenance to ensure
worker safety and environmental protection.
Heat pump:
A heat pump is a device that transfers
heat from one location to another using a refrigeration cycle. It can be used
for both heating and cooling purposes and is considered an energy-efficient alternative
to traditional heating and cooling systems.
Here are the key components and functions of a
heat pump:
·
Evaporator: The
evaporator is located indoors or outdoors, depending on the type of heat pump
system. It absorbs heat from the surrounding air, water, or ground (depending
on the heat source) and converts it into a low-pressure gas refrigerant.
·
Compressor: The
compressor is responsible for increasing the pressure and temperature of the
refrigerant gas. It pumps the refrigerant through the system, creating a
high-pressure, high-temperature gas.
·
Condenser: The
condenser is typically located indoors or outdoors, opposite to the evaporator.
It transfers the heat from the refrigerant to the desired space or water
source. When the heat pump is in heating mode, the condenser releases the heat
into the indoor environment. In cooling mode, the condenser releases heat to
the outside environment.
·
Expansion Valve: The
expansion valve controls the flow of refrigerant into the evaporator. It
reduces the pressure and temperature of the refrigerant, allowing it to absorb
heat from the heat source.
·
Reversing Valve (in
some systems): A reversing valve is present in heat pumps that offer both
heating and cooling capabilities. It allows the refrigerant flow to be
reversed, changing the direction of heat transfer. In heating mode, the
reversing valve directs the refrigerant to extract heat from the heat source
and release it into the indoor space. In cooling mode, it reverses the process,
extracting heat from the indoor space and releasing it outdoors.
·
Heat Distribution
System: The heat pump is connected to a heat distribution system, which can be
in the form of air ducts, radiant floor heating, or a hydronic system. This
system distributes the heated or cooled air or water to different areas of the
building.
Heat pumps can utilize various heat sources,
including:
·
Air Source Heat Pump
(ASHP): ASHPs extract heat from the ambient air and transfer it indoors during
heating mode or outdoors during cooling mode.
·
Ground Source Heat
Pump (GSHP) or Geothermal Heat Pump: GSHPs extract heat from the ground through
a ground loop system buried underground. The ground temperature remains
relatively stable, providing a consistent heat source.
· Water Source Heat Pump (WSHP): WSHPs extract heat from a water source, such as a lake, river, or well, for heating or cooling purposes.
Heat pumps offer several advantages,
including energy efficiency, lower operating costs compared to traditional
systems, and the ability to provide both heating and cooling. They are
particularly effective in moderate climates but can also be used in colder
regions with appropriate design and auxiliary heating systems. Proper sizing,
installation, and regular maintenance are essential for optimal performance and
efficiency of heat pump systems.
Heat exchangers:
A heat exchanger is a device designed to
efficiently transfer heat between two or more fluids, without them coming into
direct contact with each other. Heat exchangers are widely used in various
industries and applications to facilitate heat transfer and improve energy efficiency.
Here are the key components and functions of a
typical heat exchanger:
·
Tubes or Plates:
Heat exchangers consist of a series of tubes or plates that provide a large
surface area for heat transfer. These tubes or plates are typically made of
materials with good thermal conductivity, such as copper, aluminum, stainless
steel, or titanium.
·
Hot Fluid and Cold
Fluid: Heat exchangers have two separate fluid streams: the hot fluid and the
cold fluid. The hot fluid transfers its heat to the cold fluid through the heat
exchanger.
·
Flow Channels: The
hot and cold fluids flow through separate channels within the heat exchanger.
The flow channels can be either parallel or counter-flow configuration.
·
Heat Transfer
Surface: The heat transfer surface is the area where the hot and cold fluids
come into close proximity to facilitate heat exchange. This surface can be
either the walls of the tubes or the plates in plate heat exchangers.
·
Shell and Tube: In a
shell and tube heat exchanger, the hot fluid flows through the tubes, while the
cold fluid circulates around the tubes within the shell. The heat is
transferred through the tube walls to the colder fluid.
·
Plate Heat
Exchanger: Plate heat exchangers consist of a series of corrugated metal plates
stacked together. The hot and cold fluids flow through alternate channels
between the plates, allowing efficient heat transfer.
·
Fins (in some heat
exchangers): Fins are extended surfaces attached to the heat transfer surface
to enhance heat transfer by increasing the surface area and promoting better
airflow or fluid flow.
·
Baffles: Baffles are
internal devices within the heat exchanger that help direct the fluid flow and
promote turbulence, improving heat transfer efficiency.
The efficiency and performance of a heat
exchanger depend on factors such as the design, surface area, flow rates, fluid
properties, and temperature differences between the hot and cold fluids.
Different types of heat exchangers, such as shell and tube, plate, or finned,
are selected based on specific application requirements, including temperature
range, pressure, flow rate, and the nature of the fluids being exchanged.
Heat exchangers are used in various industries, including HVAC (heating, ventilation, and air conditioning), power generation, chemical processing, oil and gas, refrigeration, food and beverage, and many others. They play a critical role in improving energy efficiency, reducing operating costs, and facilitating heat recovery in industrial processes.